Quality
Quality and product safety are the most important prerequisites for APG. Therefore we have globally standardized and established an Integrated Quality Management System across our site. This enables us to fulfill and surpass our customers’ quality expectations.
Continuous Improvement
The APG team is highly qualified and always striving for improvement and increased quality and efficiency. We do not settle for average performance. On our way to constant improvement, we rely on various initiatives like:
- APGideas management: Our internal improvement process fo APG employees.
- CAPA: We implemented this structured method for solving problem and identifying causes.
- Plan do check act (PDCA): A structured approach for dealing with problems, difficulties, changes, risks and opportunities.
- Training & qualification of the employees: Group-wide, cross- factory advanced training promotes the competence and
qualification of the employees. - Zero-error strategy: Our corporate culture, the employee attitude, and our standards all support error-free processes and products.
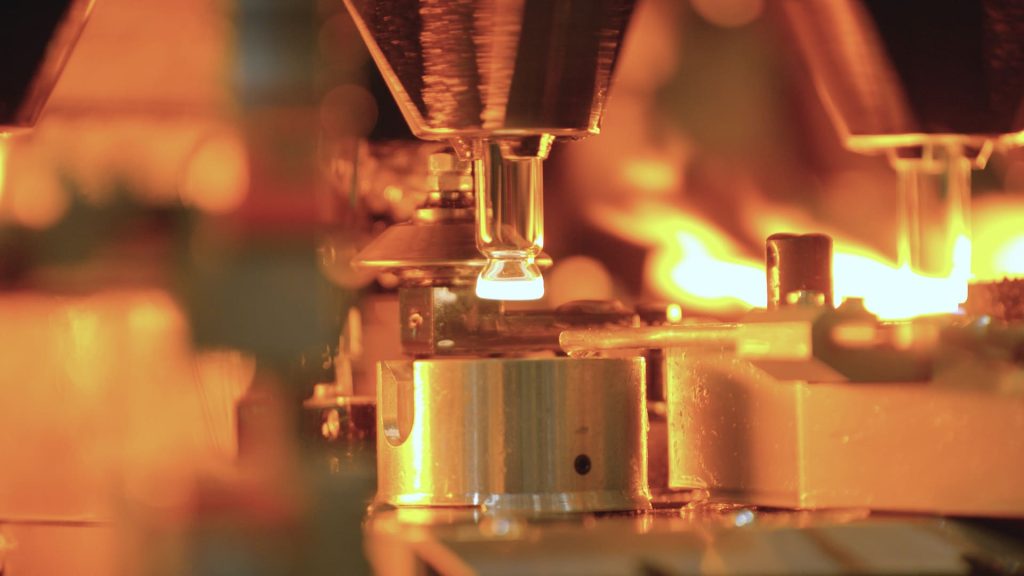
Quality Control
Automated and manual quality controls start right in the Hot End section. After being cooled down slowly in the annealing lehr, all bottles pass a vast array of state-of-the-art inspection machines at the Cold End. Additional checks are done by our operators in regular intervals.
Process capability: APG commits themselves to the constant
improvement of its process capability. Expert employees, as well as digitization and continuous improvement plans, shall support us in this endeavor.
State-of-the-art technology: Significant investments ensure that all sites are equipped with state-of-the-art inspection and production machines.
Integrated Quality Management System
Quality processes are standardized across our plant in order to ensure that our products are manufactured in highest quality:
- ISO 9001 (Quality Management)
- ISO 15378 (GMP)
Quality In Processes And Products
- Quality inspections in accordance with the European, and US- pharmacopeia
- Regular checks of heavy metal content
- Microbiological and particle testings
- Comprehensive quality controls with state-of-the-art inspection machines
- Top-class, cutting-edge production and quality testing facilities
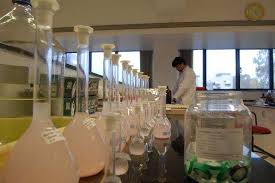
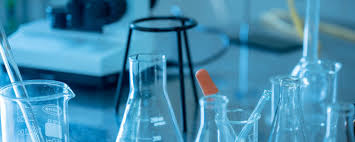